Tony Smith: Paddleboard Passion
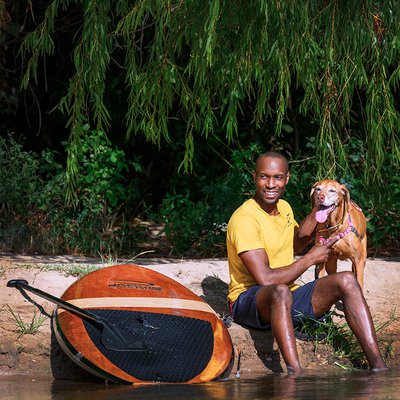
Gliding on top of the water in a canoe, kayak or on a paddle board...a person can get close to nature in a way that's just not possible on dry land. On the podcast, meet a man whose passion for paddling changed the course of his life while also making time on the water more enjoyable for others.
Tony Smith: Paddleboard Passion
Season 3 Episode 8
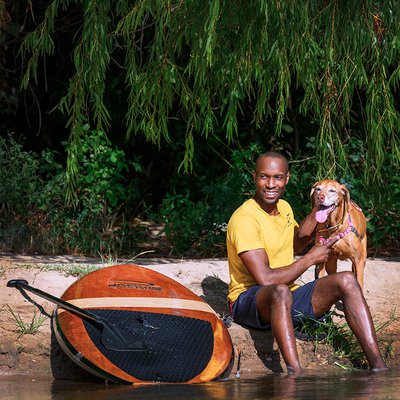
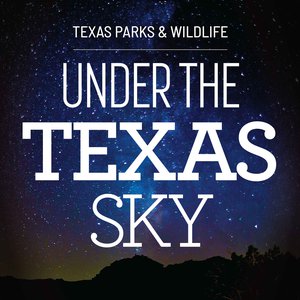
UTTS: S2E8: TONY SMITH: PADDLEBOARD PASSION
[MUS—FRIENDS OF THE EARTH]
[SFX—PADDLE / BIRDS]
Gliding on top of the water in a canoe, kayak or paddle board ... a person can get close to nature in a way that's just not possible on dry land. We have miles of inland and coastal paddling trails in Texas just waiting for you to put in.
Coming up on the podcast, we meet a man... whose passion for paddling changed the course of his life... while also making time on the water more enjoyable... for others.
Stay with us.
[MUS—HOWDY]
From Texas Parks and Wildlife....this is Under the Texas Sky...a podcast about nature...and people...and the connection they share. I'm Cecilia Nasti.
Of all the sounds you'll hear in nature...
[SFX—CHOP SAW]
THAT is not one of them—at least it won't be made by nature. But this particular sound is a precursor to helping people to spend time outdoors on the water. And it echoes off the walls in an unassuming single-story warehouse... in an industrial park on the fringes of Austin, Texas...by this guy.
[TONY SMITH] Hi. I'm Tony Smith., I'm the founder of Jarvis Boards, and we build hand crafted wood stand up paddleboard, surfboards and wake surfboards right here in Austin, Texas.
[MUS—ONCE IN A WHILE]
Tony Smith was the kind of kid that loved to build things. He'd also had a penchant for dismantling and reassembling, whatever came across his path. He loved understanding how things worked and creating with his hands.
Add to that: he had a taste for the outdoors which took root early in life.
[TONY SMITH] We grew up in Houston and so we would go down and go fishing—my brothers, my parents; all the time. We just loved being around the water. Later in life, in college, I started surfing and really fell in love with that, hence, wanting to build paddleboards and surfboards in the first place.
Building paddle boards full-time didn't happen overnight. Tony earned a degree in finance, and after graduating university, he spent his days in an office environment instead of a natural environment. He eventually became a successful stockbroker and says it was a demanding yet rewarding career that he loved.
[MUS—BUNGALOW SERENITY]
Despite his success, Tony felt a yearning. He missed using his hands to build things as he had when he was younger. He wanted to rediscover his 10-year old self.
So, on a whim, he bought a how-to guide for building a cedar strip wood canoe at a local bookstore. He says the plan was to build a canoe first to learn the ropes... and then build a wooden sea kayak.
Building the canoe became a welcome stress reliever for Tony Smith ...who was beginning to feel a bit ...burnt out... from his high stress job.
He said he probably made every mistake possible during the process, but loved the distraction... and the result of his efforts.
Because after the sawdust settled, he had a beautiful and functional piece of art, which drew the attention of onlookers... whenever he took it out on Lady Bird Lake in Austin with his wife and their family dog.
The success he had with the canoe whet his appetite for trying his hand at building other watercraft; it wasn't long before he was spending nearly all his free time in his garage... constructing wooden stand up paddleboards for personal enjoyment. He'd become enamored of paddle boarding on his honeymoon in Costa Rica.
Friends and neighbors took notice of his handiwork and wanted Tony to make boards for them, too.
In no time, found himself running a part-time business he hadn't planned, helping people get outdoors and onto the water.
[TONY & CECILIA] Yeah, so it was interesting; for several years I straddled the fence. I would work in finance, come here on my lunch breaks ... come here to the shop after work, nights, weekends—sometimes until one in the morning. Working on wood boards, and it just got too much after awhile. And sort of had to take a leap of faith and go for the paddleboards full time, and, yeah, here we are a few years later.
[CECILIA] Well, how was that for you when you finally did take that leap of faith, and you had to decide one or the other?
[TONY] It was nerve-wracking, right? I loved the company the company I was working for: it was a great job, stable career, absolutely loved it, loved the people. But it was that nagging question of "what if," right? And I didn't want to live with that what if I could have made it, and so the real big sort of "ah ha" moment where I knew I had to flip the switch: I came here on my lunch break one day. Did a little bit of work, zipped back to the office, and my Admin said, ‘Dude—you have sawdust all over the back of your suit.’ And I knew then, it’s time to make that decision to go for it and haven’t looked back since.
[MUS—OF NEW BEGINNINGS]
Tony Smith made his first wooden paddleboard in 2012 and officially launched Jarvis Boards shortly thereafter, using his middle name for the business.
I met Tony one afternoon in late spring at his warehouse workshop in Southeast Austin, just a couple of miles from Texas Parks and Wildlife headquarters. Upbeat, fit and muscular, this African-American millennial man knows who he is and what he wants from life.
His workshop consists of four rooms; working with his team...the work of cutting, glue up, assembly, shaping and sanding takes place in the largest room in the building; meanwhile, in a smaller, adjoining area they waterproof and glass the boards; glass is his shorthand for fiberglass.
[TONY SMITH & CECILIA] Yeah, so this side of the shop we'll do the majority of the woodworking and sanding down of the boards.
So, this is a big part of like where the boards are born. We'll mill down the wood on the band saw here. Alright, so we will just line the band saw blade up; that's about where we want it...turn off the safety switch...and here we go...
A band saw is a cutting tool where a band of steel with teeth rotates on two wheels and passes through a table. The saw has guides and bearings located above and below the blade hold it in position as it cuts. Tony used it to cut a piece of cedar in half to use as tail blocks on the board he was working on before I arrived.
[CECILIA] And so, about how thick do you cut pieces for this?
[TONY] It depends on the board that we're making and the piece of wood. So, you know, the boards—some of them—have as many as 20 different pieces of wood. The nose and tail blocks that we use are about two inches thick, that not only looks unique cosmetically, it also provides a lot of impact resistance. So, think of an epoxy coating over a hardwood floor versus epoxy over a Styrofoam cooler. And that's sort of the durability difference, if you will. And so, that's why surfers originally, back in the day, started putting wood on the nose and tails of the boards.
[CECILIA] Look at me learning things.
[TONY] Alright, so we cut this raw piece of wood down to two thinner strips that we can then glue up into a tail block.
Once the raw wood's been ripped, he uses a chop saw to cut it down to size.
[CECILIA] As easy as that; just like cutting through butter.
[TONY] Yeah, just like cutting through butter, you don't want your finger close to that.
[CECILIA] And I see that you have will of yours.
[TONY] I do have all of mine. Thank goodness. Don't jinx it.
[CECILIA] Oh. Sorry!
[TONY] Obviously the boards that we make they're all hand crafted right here in Austin; and you don't want the wood touching the water. So, to make the board waterproof, we take it over to the next room over which is where we do the fiberglass coating on the board, which makes a permanent bond; you don't have to refinish it or do anything like that to reseal the wood. Once you laminate it, it's done and it's a durable product it'll be...you'll get years of use. So, cool. I'll show you that room.
[TONY] So... watch your step.
[CECILIA] Uh yeah, I know, I.
[TONY] Sorry...
Tony and I wove our way through stacks of lumber...electrical cords...work benches, and bales of Styrofoam until we reached the door to the next room.
[TONY] Uh...so...in this room, uh, as I said, we'll do the fiber-glassing. And it starts with this...it looks like just cloth, right? It's flexible. It's pliable. We'll roll this out on the wood. We'll then mix up some two-part epoxy, uh, and spread it—covering the entirety of the board...um, permanently bonding the wood with the fiberglass. So it's a lot of skill and practice that goes into making that permanent bond, uh you know, not only look really good, so you can see the wood grains of the wood, um, but also make it strong and structural as well. The cool thing about doing it is when you are in this stage it's when the wood really comes to life. So you can see the wood grain. You can see the knots in the wood, um, and you can really see the uniqueness of that given board that you're building.
[CECILIA] And this isn't the only thing you do.
[TONY] Um, so, paddleboards have been our bread and butter. We recently introduced wood surf wake boards and wood surfboards as well. Um, it's just, you know, been fun. And one of the cool things about what we do is that we build a lot of custom boards. So, customers will come to us and ask for a board for a graduation or an anniversary or retirement. And, we'll laminate the individual's name, or date or whatever's significant to that person and make that personalized product for them. That's what's really cool; we get to engage with them, learn their story and get to be a part of all of these different life journeys of individuals around the world.
Most modern day stand up paddle boards are mass-produced... and constructed solely of manmade materials... like foam or plastic; some are even inflatable. Tony's handcrafted paddle boards are hollow-core wooden vessels.
[TONY & CECILIA]
[TONY] The wood—it's not just cosmetic. It adds a tremendous amount of impact resistance and strength and rigidity to the board. And so because of that, we're able to use less of the epoxy and the fiberglass than standard boards use.
[CECILIA] And what kinds of woods are you using.
[TONY] So, it varies. Primarily we use a lot of cedar, maple, and cherry—and then we've done some hemlock, walnut and some exotic woods as well, like fabinga and other cool stuff as requested.
He said he especially likes using cedar because it's a "dream" to work with, even though it makes him sneeze.
[MUS—[PERUVIAN MUSIC]
While paddle boards have gained popularity over the past two decades, these conveyances have an ancient lineage.
More than two thousand years ago... Peruvian fishermen were believed to have used a kind of stand up board made of reeds that were tightly bound together with ropes made of organic fibers.
We've come a long way since then.
[06—TONY & CECILIA]
[TONY] So, once the board's fully glued up, it's sort of a bunch of different raw wood pieces with a recycled Styrofoam core. It then all needs to be sanded down to a finished shape. That takes a fair number of hours. So, what we'll do is sand down one of those boards.
[CECILIA] Go for it.
Tony pulled a nearly finished board from one bench onto another for sanding. The board towered over him when he held it vertically.
[CECILIA] It looks too big for you to carry.
[TONY] No. So there...this one actually isn't one of the big ones. They're really lightweight and we put a handle in the middle that's ergonomic that makes it pretty easy for you to wrap your hand around and carry it just kind of on your hip, if you will.
[CECILIA] Okay.
[TONY] Alright, so this board, you can see where the wood nose and tail box that we cut a second ago would look like this. And so to sand it down we'll take one of our hand orbital sanders, fire it up and literally sand it down until we get it to the right shape.
[CECILIA] Make it so...
[TONY] Make it so, Yeah, that's it. Alright, Here we go...
With the business end of the orbital sander, Tony used long, smooth movements along the entire length of the board to ensure an even surface, free of ridges and rippling. I could not help but run my hand over it when he was done.
[CECILIA] And it's so silky.
[TONY] Yeah, and it ends up when we're done with it, the wood is really smooth. Once we have it all sanded down and have the shape how we want it, we'd then take it to the next room and roll out that fiberglass cloth, and cover the entire board to waterproof the entire board, if you will.
[CECILIA] Okay. And I see all this Styrofoam here. What is that used for?
[TONY] Yeah, so we will use, on the inside of the board, a recycled Styrofoam core. That's what help keeps the board lightweight. And then, we'll also use that same recycled Styrofoam as packaging for the products that we ship out to make sure they get where they're going safely.
[MUS—HATE AT FIRST SIGHT]
Following his heart and his love of the outdoors, Tony Smith of Jarvis Boards created a fulfilling life around handcrafting paddleboards so others can experience the wonder of gliding on the water in harmony with nature while making memories to last a lifetime.
[TONY] You know, I started building these boards for my own personal use and enjoyment. It's really taken me aback how much I have enjoyed connecting with the individuals that have purchased our boards, and literally seeing on Instagram somebody in California or Michigan or Switzerland out paddling with their family and making those family memories. It's really cool for me personally, because I feel like I am a small part of that. So, I hope it becomes sort of an heirloom piece, if youwill that they can use, love and enjoy for a long time and make great family memories, and hopefully inspire them to go out and do something cool as well.
[MUS—DANCE WITH ME]
Whether you use a paddle board, canoe or kayak, Texas Parks and Wildlife has resources to help get you on the water. Visit its Texas Paddling Trail page. Before going to any Texas state park, natural area or historic site, check the website for updates or call the site directly. One more thing—remember to wear a lifejacket when you are on the water.
[MUS—TO ORBIT YOUR SOUL]
And so, we come to the end of another podcast. Under the Texas Sky is a production of Texas Parks and Wildlife and is available at UndertheTexasSky.org or wherever you get your podcasts.
We record the podcast at The Block House in Austin, Texas. Joel Block does our sound design. Randall Maxwell is our associate producer.
Susan Griswold and Benjamin Kailing provide distribution and web help, and Whitney Bishop does our social media.
I’m your producer and host, Cecilia Nasti, reminding you that life’s better outside when you’re Under the Texas Sky.
[TONY] I came here on my lunch break one day. Did a little bit of work, zipped back to the office, and my Admin said, ‘Dude—you have sawdust all over the back of your suit.’ And I knew then, it’s time to make that decision to go for it and haven’t looked back since.
Join us again next time for Under the Texas Sky.